- AZTF
- Posts
- Mesa-Based Rosotics Revolutionizes Aerospace with Magnetic Field 3D Printing
Mesa-Based Rosotics Revolutionizes Aerospace with Magnetic Field 3D Printing
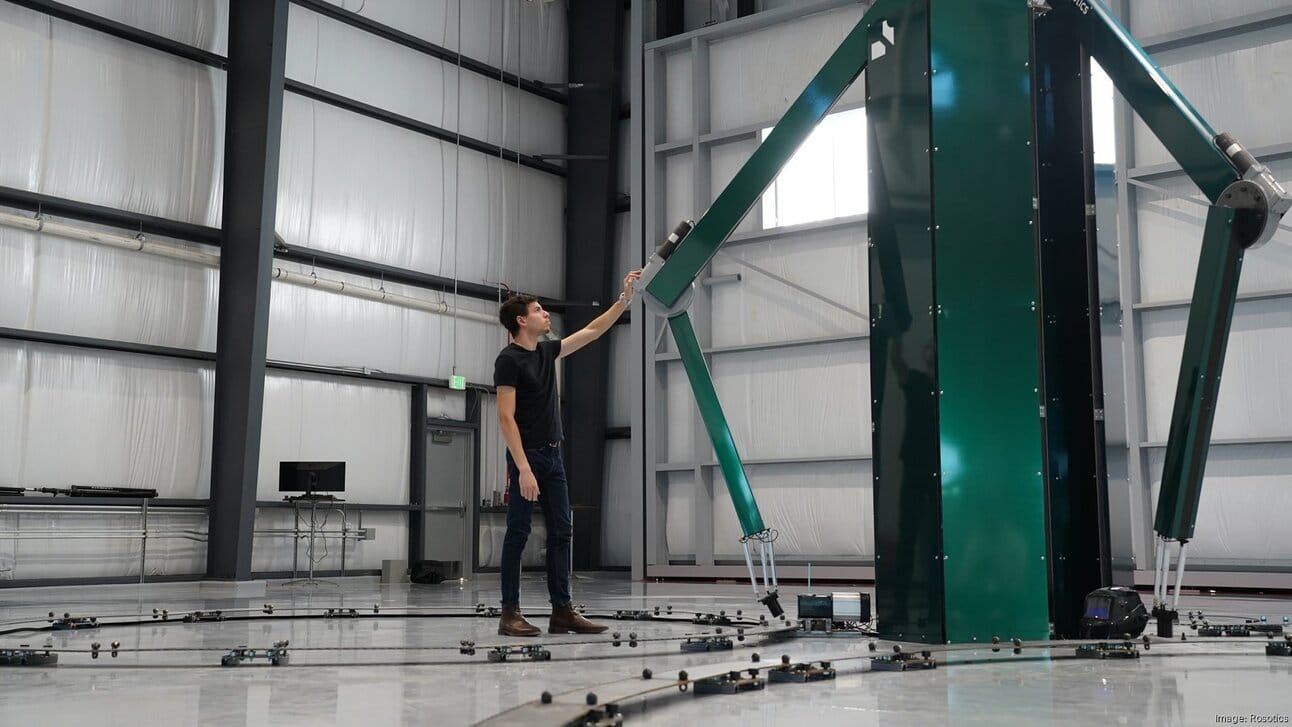
In a landmark advancement for aerospace manufacturing, Mesa, Arizona-based company, Rosotics, is gearing up to make waves in the industry with its novel 3D printer, the Mantis. This new technology, shunning traditional high-power laser methods, employs magnetic fields to heat metal feedstock — a groundbreaking approach set to redefine large-scale aerospace construction.
Rosotics co-founder and CEO, Christian LaRosa, shared with SpaceNews the efficiency of their proprietary technique, saying, “You get the same end result without the laser in that process.” The company’s triumph is in the power; the Mantis operates on a mere 240-volt outlet, a significant stride in operational efficiency.
With anticipation building, Rosotics aims to initiate the delivery of the Mantis by the third quarter of 2023. Customers keen on this technology can secure their order with a $95,000 deposit and an agreement to a hardware-as-a-service contract. Beyond simply handing over the hardware, Rosotics promises comprehensive support including installation, maintenance, and future upgrades at no additional cost.

The Mantis isn’t restricted in its capabilities. It’s engineered to adapt to various applications, providing a starting configuration featuring a single printhead capable of additively manufacturing aluminum or steel structures with diameters ranging from 1.5 to 8 meters.
Rosotics unveiled their impressive Mantis prototype on March 24, hot on the heels of Relativity’s launch of the 3D-printed Terran 1 rocket. “Relativity has developed this capability for themselves,” LaRosa noted, “We’ve been focused on creating a new form of metal additive [manufacturing] that will reduce the difficulty in getting 3D printing implemented in fields like aerospace.”
Jim Cantrell of Phantom Space, a Tucson-based company, acknowledges the potential merits of the Mantis for launch vehicle manufacturers but stipulates that consistent metallurgical properties are key. The sentiment is cautious yet optimistic.
Beyond aerospace, Rosotics unveiled insights during New York Tech Week that highlighted their expansion into maritime applications. Their experience with high-performance aerospace materials, garnered through their M1 Printer, feeds into their strategic plan to push into naval operational deployment by 2025. Utilizing Rapid Induction Live Interpass (RILI) technology — a potent alternative to laser-based systems — Rosotics is on track to fabricate robust structures designed for the demanding marine environment.
Metal 3D printing at this magnitude is a complex endeavor, with industry leaders like Desktop Metal and Markforged spearheading smaller-scale production. Rosotics, under Christian LaRosa’s direction, however, dreams bigger. With his rich background in aerospace engineering and bionics, LaRosa brings a unique perspective to the challenges plaguing metal 3D printing — challenges he’s tackling head-on with entrepreneurial vigor and a knack for breaking down daunting problems

Christian LaRosa’s day-to-day life oscillates between technical development and the broader operational demands of running a company on the cutting edge. His passion for his craft coupled with strategic acumen guides the team at Rosotics to incrementally conquer the mammoth task of shifting the paradigms of metal 3D printing.
With the ambition of decentralizing manufacturing and entering diverse markets like aerospace, space, and marine sectors, Rosotics looks towards a future enriched by its technologies. It’s a future where every nut and bolt is a testament to innovation, efficiency, and the relentless pursuit of a world where ambitious dreams of metal 3D printing become tangible realities.